
Major Requirements for Type 4 Composite CNG Cylinders: Innovation, Low Cost, and Commitment to Excellence
The rapidly growing international market for natural gas vehicles (NGV’s) is creating a tremendous need for lightweight, reliable CNG fuel tanks. Industry pioneers like Lincoln Composites , Quantum Fuel Systems, and Ullit have spent years and tremendous energy to design, produce, and sell safe, world-class Type 4 fully composite CNG cylinders. During the last few years, new factories have been springing up around the world to expand the technology for composite CNG cylinders. The best cylinder manufacturers have learned the major requirements for success: innovation, low cost, and an unswerving commitment to excellence and safety.
Cost Reduction from intelligent material selection. Plastic liners offer the opportunity for substantial cost reduction from Type 3 aluminum-lined composite cylinders. Common plastic liners of HDPE, HDPEX, and polyamide (Nylon) are much less expensive to build than seamless aluminum or steel liners. Carbon fiber laminates, the most popular choice for strength and weight, comprise about 65% of total manufacturing costs. Intelligent strategies for reinforcement method and fiber selection allow the cylinder costs to be minimized. Good design helps reduce the costs and weights of composite CNG tanks.
The greatest difficulty: connection of metallic necks to plastic liners. Metallic necks and end pieces are used to withstand the extreme force of internal pressure against the valves. The most difficult part of Type 4 cylinders is to create an infallible seal to hold gases at high pressures, extreme temperatures, and demanding services conditions. Lincoln, Ullit, and some others create high strength adhesive bonds between plastic and metal during the molding process. Most of the other manufacturers use some type of mechanical compression methods using O-ring seals or similar materials.
Composite laminate: must design for damage protection. Carbon/epoxy composites have excellent burst strength but are relatively fragile. Some type of additional protection is required to improve damage resistance from fire and extreme heat, impacts, abrasion, and so forth. Lincoln Composites uses their Tuffshell® protection system; a combination of carbon/glass hybrid combined with a foam and glass/epoxy outer shell. Other manufacturers use a combination of rubber end caps with some extra outer fibers.
Plastic liners must withstand permeation and temperature extremes. Plastic formulations and wall thicknesses must be selected to withstand permeation of the gas through the liner walls. Automobile gasoline tanks, for instance, often use multiple-layer laminated molded HDPE to prevent gasoline fume permeation at simple atmospheric pressure. HDPE storing CNG at 250 bars (3600 psi) pressure must have proper thickness to keep the gas from seeping through. Additionally, the plastic must be able to withstand temperature extremes of oven curing the composite overwrap and also the extreme low temperature from venting the cylinder quickly. Type 4 CNG cylinder temperatures can drop from 20C to -50C when CNG is vented quickly from 250 bars to 0. The extreme cold temperatures are a major challenge for almost any plastic.
Successful manufacturers combine innovation with an extreme commitment to quality and safety. Many manufacturers of Type 4 composite CNG cylinders have started, failed, and disappeared. The successful manufacturers use innovation and expert engineering strategies to design extreme safety features with efficient, high quality manufacturing. Lincoln Composites, for instance, uses many excellent design features that – to other company managers – often seem too expensive and excessively cautious. However, Lincoln’s commitment and hard work have paid off. They are the most successful and longest lasting manufacturer of Type 4 composite cylinders. Lincoln’s success comes from their excellent engineering and management.
Designing or testing type 4 composite cylinders? Hansho’s experts can help. Hansho’s engineers have been designing, testing, and building fully wrapped composite pressure vessels since 1982. We have helped provide technology and factory start-up services for more than 19 composite cylinder factories in 8 countries. Hansho provides technology services and machines for design, testing, and manufacturing composite CNG cylinders. Contact sales@hansho.com for more information.
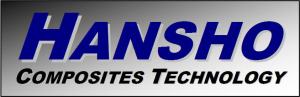
www.hansho.com
Phone: +1 714-795-2320
Technorati Tags: Lincoln Composites Composite Cylinder CNG Type 4 Composite Cylinder CNG-4 ISO 11439 Carbon Fiber Hansho Composites